泡泡图文视频解读:显卡是怎样炼成的
提起显卡,大家首先想到的就是GPU、显存、频率、板型、用料等等,没错,一块显卡最重要的部分也就是这些,相信很多玩家对此都是倒背如流,甚至对于GPU的架构规格、显存的种类速度、电容的类型特性、公版和非公版的优劣这些更深层次的内容也都了如指掌。
但要谈到GPU、显存、电容、PCB这些元件是如何组装起来,成为我们手中功能完备的显卡,想必大部分人对此都比较陌生。俗话说,知其然还要知其所以然,在大家厌倦了显卡的跑分测试、对微小的FPS差距提不起兴趣的时候,不妨坐下来慢慢阅读本文,来仔细了解3D游戏必备之物——显卡是怎样炼成的!
显卡的设计和制造是各自独立的:NVIDIA和AMD设计GPU,然后由台积电或联电代工GPU;显卡PCB设计主要是一些AIC和AIB的研发部门,而显卡制造则是交给那些大型代工厂来完成。GPU并不是随便就能更改设计的,而PCB大多都是公版或者在公版的基础上进行二次开发,所以显卡的制造环节就显得尤为重要。
与GPU设计和PCB设计相比,显卡制造看起来技术含量要低一点,但需要投入大量资本,而且对于设备、流程、监控体系和质量认证方面都有极高的要求,所以大多数显卡厂商都没有自己的工厂,需要找有实力的工厂进行代工或者直接OEM。因此无论显卡设计还是制造,都是非常重要的环节,不同的公司各有所长、分工明确。
柏能(PC Partner)是全球最大的显卡代工厂,它为ATI和蓝宝石代工显卡相信很多人都清楚,除此之外柏能几乎为国内所有的整机厂商代工显卡,在欧洲的OEM业务更是源源不断,出货量遥遥领先。但由于柏能没有自有品牌的显卡,因此一直以来都显得很低调,大多数人都不了解这家国际知名的香港公司。
从06年底面向全球推出自有NV显卡品牌ZOTAC(索泰),到今年7月索泰显卡在国内全面上市,栢能科技从幕后走向前台大举入侵零售市场。依托栢能科技的工厂背景,索泰显卡具备那些没有生产能力的通路商所不具备的各种优势,由此可以在提供品质最好的产品的同时,同样能在价格上拥有竞争力。
为了进一步探寻柏能科技和索泰的实力,泡泡网特意对国际一流化的柏能工厂进行实地采访。如果您对此感兴趣的话,就跟随我们DC和DV的镜头,进入复杂的生产线,来深度了解显卡的生产过程。
可能很多人都有这样的疑问:主板的面积比显卡大很多,上面集成的芯片少说也有10多颗,密密麻麻的元件更是数不胜数,还有那么多的插槽和接口,为什么显卡卖得比主板还要贵呢?
● 显卡虽小、五脏俱全,成本比主板还要高
这个问题的原因来自于多方面,最大的因素就是显卡上集成了GPU和显存这两种高集成度的芯片,GPU的晶体管数远大于CPU,显存的速度远超内存,其成本自然很高。而主板上南桥和北桥芯片复杂程度远不如GPU,其它功能芯片更加简单、成本也相对较低。
华硕Striker Extreme为8层PCB ATI HD 2900XT多达14层PCB
另外,显卡的PCB面积看似远小于主板,实际上PCB布线的复杂度和集成度有过之而无不及,低端显卡最起码的要求就是4层PCB、中端为6层或8层、高端10层和12层甚至14层都开始投入使用。一般来说PCB的成本和面积成正比,而和层数是几何级数的关系。绝大多数主板都是4层PCB,一些以超频为卖点的高端主板是6层,使用8层/10层的主板则是屈指可数,不具备普遍性。因此中高端显卡的PCB成本也是要高于同档次主板的。
最后,大多数人会认为主板上的电子元件数量要超过显卡,实际上也要分高低端来说。一般低端显卡有200-400个料件,中端显卡是500-700左右,高端显卡在1000个左右,旗舰显卡可达1200个!大家应该很容易就能注意到显卡正反两面的电子元件都是密密麻麻,主板虽然PCB面积非常大,但元件并不像显卡那么密集,而且PCB背面的元件一般都非常少,所以大多数主板的料件数在600左右,也就是中高端显卡的水平。
对于板卡加工厂来说,制造工序和制造成本基本上取决于料件数目,因为每台SMT贴片机所能安装的元件数目基本是固定的,料件数目越大,所需工序和时间就越多,而且良品率会比较低,所要经过的检验和测试步骤将会更多。因此,很多时候主流中高端主板和显卡的制造成本是差不多的。
● 显卡制造流程揭秘
了解了以上资料之后,相信很多人都对显卡的生产制造过程非常感兴趣,下面我们就来看看一块显卡从原料变为成品到底需要多少步骤:
上图就列出了全球最大显卡代工厂——柏能科技对于加工显卡时的全部流程,下面就通过栢能工厂的实际设备和生产线来详细了解显卡是怎样炼成的。
● 第一步:来料检查
首先要准备好原材料,主要包括GPU、显存、PCB、电容、电阻、电感等等。这部分工作是在一个完全封闭的实验室中进行,对于环境的要求非常高,工作人员需要对芯片和元件进行仔细检查把关,确保从源头杜绝劣质原料进入生产线。
对于PCB的检查除了人工检验之外,还会通过专用的设备记录各种信息和日期,每一片进入生产线的PCB都会有一个唯一的代码,这样就能够实时监控到PCB目前正在哪个位置进行加工。即便是加工完成之后,也能通过条码了解到是哪套设备曾经在什么时间加工过它,这样一旦出现意外问题时,就能很快地查找到原因和出故障的设备,并且对同批次的显卡进行全面检查。
● 第二步:印锡浆
PCB只是一块电路板,电子元件和PCB的接触固定全靠焊锡,因此接下来就需要将锡浆印到PCB板上。
印锡膏机的原理有些类似于油印机,每一款PCB都对应一种有固定孔位的钢板(相当于蜡纸),然后锡膏刷就能在PCB的对应焊点留下痕迹,而其他位置则会被钢板遮挡不会有焊锡。
这样印上去的锡膏主要是针对SMT贴片机,因为下一道工序就是在PCB上“粘贴”各种贴片元件。
我们都知道PCB分为正反两面,一般显卡PCB背面的元件甚至要比正面多一些,而且背面大多是一些小元件,所以上料的顺序就是先背面后正面、先小后大、最娇嫩的GPU会在最后安装。
● 第三步:进入SMT贴片机阵列
PCB经过印锡之后,就可以开始往上面粘贴电子元件了,一块显卡上可能有成百上千个电子元件,种类也是五花八门,因此在生产流程中要经过许多个SMT贴片机,每个贴片机都要负责数十种元件的贴片任务。
-
小电容、小电阻、三极管等小件高速安装
上面这台机器就是用四台相同的SMT拾放机组合而成,每一台都可以安装几种或十几种小电容或者电阻。这四台机器虽然完全相同,但可以分别设定PCB的什么位置安装什么元件,然后机器就会按照设计图和型号全自动安装。
这是最新购置的Fuji NXT M3S模块组合式SMT拾/放机,总共拼接了8台小型机和1台大型机,这些组合方式都是按照加工显卡的要求而定的,低端显卡和高端显卡自然有不同的待遇。
也有一些大型贴片机最多可以安装50种以上的元件,但由于存在资源浪费的情况(比如大量生产低端显卡)、而且效率不高,因此逐渐被组合式贴片机所取代。工厂可以随时分拆组合这些贴片机,以适应不同显卡的生产需要,最大限度的利用工厂设备资源。
泡泡网:国内最强显卡代工厂探秘 之 SMT高速贴片机
通过上面这段视频就可以了解到SMT贴片机的工作方式,感觉有点类似于缝纫机,这些小元件的安装速度极快,但由于数量庞大,因此也要耗费不少时间。
显卡PCB上的小型贴片元件,比如密密麻麻的贴片电阻、电容、二极管、三极管等都是通过以上SMT贴片机“粘”在上面,一台SMT可以同时粘贴十几种小型元件,但一些大型的元件,比如GPU、显存、控制芯片等需要使用专用的贴片机安装。
接上页,SMT需要经过很多工序,按照先小后大的原则,接下来就要在显卡正面安装一些大型贴片元件了。
● 第三步:进入SMT贴片机阵列
-
GPU、显存、控制芯片、贴片式电容、电感等大件精确安装
上面这台机器可以安装10多种元件,大家一眼可以看清楚的就是GPU,其它元件相信大家也会比较熟悉:
正在生产的是一块X1950PRO(或GT)显卡,GPU和供电部分的一些大件都是一起安装的。当然,这些大件的安装过程要稍微慢一点,并不像上一页那样看都看不清楚,还是放一段视频让大家可以一目了然:
泡泡网:国内最强显卡代工厂探秘 之 SMT安装GPU和显存
其实不论大件还是小件,安装方式虽然有所不同,但道理上完全一致。可以给大家这么一个形象的比喻,SMT贴片机就像是家用的打印机,可以给它安置各种颜色的墨盒(贴片元件),然后它就可以按照程序设定自动找到PCB相应的位置并且放上去。当然仅仅放上去还是不够的,为了让元件和PCB接触更加牢固,需要进入下一道工序——
SMT贴片机只是将元件粘在了PCB上面,两者的接触并不牢固,为了让PCB上的焊锡与元件的焊点完全融合在一起,就需要进入高温的回流焊炉:
● 第四步:过热风回流焊
这台大型的XP-M2就是回流焊炉,由于需要精确的温度控制和全程监控参数变化,所以工作的时候整台机器是全密封的。我们拍照时正好是设备检修,因此得以看清内部结构。
通过之前的SMT贴片机之后,所有的元件均已各就各位,接下来就是控制好温度,让PCB上的焊锡和元件上的焊点(锡球)水乳交融,达到无缝连接。回流焊的过程很容易理解,但它最难以把握得就是回流焊温度曲线的设定和微调,那么怎样才能更合理的整定回流焊的温度曲线呢?
要解决这个问题,我们首先要了解回流焊的工作原理。从温度曲线分析回流焊的原理:
首先PCB进入升温区(干燥区),锡膏中的溶剂、气体蒸发掉,同时锡膏中的助焊剂润湿焊盘、元器件端头和引脚,锡膏软化、塌落、覆盖了焊盘、元器件端头和引脚与氧气隔离;
接着PCB进入保温区,PCB和元器件得到充分的预热,以防PCB突然进入焊接高温区而损坏PCB和元器件;
然后PCB进入焊接区,温度迅速上升使锡膏达到熔化状态,液态焊锡对PCB的焊盘、元器件端头和引脚润湿、扩散、漫流或回流混合形成焊锡接点;
最后PCB进入冷却区,使焊点凝固。此时整个回流焊过程结束,XPM2这台回流焊炉如此巨大,就是因为要经过四个过程。
像这种大型回流焊炉大概有十几个温区,上下一共有二十多个加热器同步加热,由此得以精确控制PCB在各个阶段的温度。而冷却区使用水冷,PCB的轨道宽度与速度都用软件控制,全自动调节。而且在设定炉温时还可以用软件自动模拟,进行生产时用软件24小时监控,这样就能够最大限度的保证焊接质量。
显卡上密密麻麻的贴片元件都是由SMT贴片机全自动安装的,但不管高端还是低端显卡不可避免的会有一些插机件,比如输出接口、供电接口等,尤其是中低端显卡会大量使用插件电容和电感,这些元件需要单独安装。
大家注意看这块半成品X1950PRO/GT,所有贴片元件通过SMT贴片机和回流焊炉之后均已安装完毕,剩下的一些空焊位就是插件电容、电感、6Pin PCI-E供电接口、DVI输出接口(VIVO部分不算),这些都在等待下一步的安装:
● 第五步:人工安装插机件
贴片元件有SMT贴片机自动安装,其实插件也有插件机,但在国内这种设备并不常见,这主要是因为插件都属于大件,人工安装的效率并不比机器差,也不容易出错,何况国内劳动力资源非常丰富且廉价,因此绝大多数工厂都使用人工安装插机件。
这里是另外的一条生产线,正在加工的是索泰8500GT显卡,低端显卡上的大件基本都是插件,可以一次性将所有插件都安装上去,节约好几道工序,而不像贴片元件那样需要多台SMT分批安装:
可以看到PCB被固定在了特殊的钢板架上,这些钢架在对应的插件孔位也有特定大小的空隙,其他位置则是密封的,这样就能直接进入下一步——波峰焊炉进行焊接。
贴片元件经过回流焊炉焊接,回流的意思其实就是再流,经过反复加热让焊点熔化进行表面焊接;而插机件要使用波峰焊炉焊接,波峰焊的原理是把融化的锡根据实际需要用气体通过焊接面的小孔吹出,黏附在PCB和插件引脚上,看上去象波峰,因此得名。
● 第六步:过波峰焊炉
早期的波峰焊为了降低焊锡熔点会使用锡铅合金作为原料,而如今由于RoHS要求无铅工艺,所以柏能工厂从2005年开始就全面启动无铅设备,我们可以看到这里的波峰焊炉使用的是锡铜银合金:
波峰焊流程:将元件插入相应的元件孔中(上一页的插机件安装)→预涂助焊剂(松香)→ 预烘(温度90-1000C,长度1-1.2m)→ 波峰焊(220-2400C)→ 切除多余插件脚→ 检查。
这其中最重要的环节就是波峰焊,它的过程简单来说就是用氮气将液态锡从底部小孔吹出,实现元器件焊端或引脚与印制板焊盘之间机械与电气连接的软钎焊。
波峰焊的真正过程我们是看不到的,上图中的显卡被固定在熔化的液态锡正上方,在显卡下部正在进行波峰焊接。虽然显卡背面的操作我们看不见,这里还是通过一段视频来了解整个过程吧:
泡泡网:国内最强显卡代工厂探秘 之 波峰焊
● 第七步:善后处理和最后的安装
-
清洗松香——免洗并不是完全不洗
波峰焊之后在显卡上或多或少会残留一些松香,这会影响的显卡的美观度,所以很多OEM客户(尤其是一些整机厂商)会要求显卡在出厂之前清洗松香:
早期的松香清洗用的助溶剂含有氟化合物,可以完全清除PCB上的残留松香,使得PCB光可照人,但氟溶剂对人体和大气都有害,目前已被取消。
泡泡网:国内最强显卡代工厂探秘 之 清洗松香
替代的方法被称为免清洗技术,但免清洗并不意味着取消原来的清洗工序,而是在清洁印制线路板及清洁的元器件、组件、部件时,采用低固体含量的新型免清洗焊剂(基外观为无色、透明、均匀、无杂物异物、无强烈刺激气味)以保证其装焊后能够达到或超过原来的清洁度水平。即符合如下免清洗三要素:1、目测外观光洁程度可接受,即仅有少量助焊剂残余或完全无残余。 2、电气特性不受影响。 3、不因环境的改变而造成不应有的腐蚀。
免清洗技术可减低清洗工序操作及机器保养成本,还可减少组板(PCBA)在移动与清洗过程中造成的伤害。助焊剂残留量现已受到控制,能通过清洁状态目视检查,完全可以配合产品外观要求使用。残留的助焊剂还可以改良其电气性能,以避免成品产生漏电,导致任何伤害。另外,免洗流程目前已通过国际上多项安全测试,证明助焊剂中的化学物质是稳定的、无腐蚀性的。
-
安装散热器
-
人工焊接特殊配件
显卡的接口部分一般都是手工焊接的,有些中高端显卡上带有附加配件,比如DVI金属屏蔽罩,这也需要一道额外的工序来安装,也是采用手工焊接的方法:
这块HD2600XT GDDR4的接口部分固定孔(注意信号针脚是波峰焊接的)就是电烙铁手工焊接,即便是8800和2900这种高端显卡也不可避免要使用人工焊接。但这些焊点并不影响显卡的电路,主要作用是固定接口,因此精度要求不高,您可以很容易分辨出这些较大的、不规则的焊点。
一般来说经过波峰焊之后,显卡上所有的芯片和元件均已到位,电路部分没有任何问题,再安装上散热器和接口挡板的话,这就是一块完整的显卡了,可以说显卡的制造过程至此已经结束。但是这样的显卡还不能直接出厂,后面还有更多的测试和检验工序等着它……
● 第八步:焊接质量检查和功能测试
-
X光探伤仪检测回流焊品质
回流焊用来焊接SMT打上去的贴片元件,这些焊点的质量无论肉眼还是通过显微镜都无法准确判断,因为焊点都在元件的下方。所以柏能工厂使用了目前非常先进的X射线探伤仪来检测回流焊品质:
泡泡网:国内最强显卡代工厂探秘 之 X射线检测焊点
X射线探伤仪是目前非常先进的检测系统,被广泛的应用在建筑、飞机、汽车等高科技和重工业领域的内部结构分析。而在这里X射线探伤仪主要用来检查GPU、显存、控制芯片等焊点比较多的元件。
一台X射线探伤仪的价格是300万,国内很多工厂都无力购买如此昂贵的设备,只能停留在目测阶段,但目测只能用来查看裸露的焊点,无法检测芯片的焊接质量。
-
目测波峰焊品质
波峰焊用来焊接插机件,这些元件体积较大,焊点都在PCB背面,只需要目测就够了。
这里需要指出的是,在显卡工厂主要有两种工作人员:穿蓝色工作服的是生产员工,穿粉红色工作服的是检验员工。生产员主要负责操纵设备、换料、上料、装配等,员工总数达2000多人;检验员主要负责检查完整性、焊接质量、以及最后的功能、性能、质量测试,这部分员工总数在1500人左右。
从生产员和检验员的人数比例中可以看出,显卡并不是装配好就完事这么简单,一块没有通过任何测试的显卡是不能出厂的,真正考验显卡的项目还有很多,对于显卡大厂来说在显卡检测方面所花的时间并不会比生产少!
-
初步测试:能否点亮,电压是否正常
显卡全部装配完毕之后,要立刻进行上机测试,只要能点亮就通过了第一关,这块显卡应该不会有什么大问题。此时需要监控显卡的各路电压,要求在标准电压限定的范围之内就合格。
-
散热器、温度测试
通过热风筒将散热器吸入空气的温度控制在38度,然后检验在此模式下散热器的工作情况和温度变化。
- 输出接口和3D测试
CRT、LCD、TV、多头输出,这些都需要进行接口兼容的测试,在测试图像输出的时候,还需要跑3DMark,来检验显卡在3D模式下的稳定性和输出品质。
此外,如今的大屏显示器非常流行,所以Dual-Link DVI和HDMI输出也是必测项目,我们可以看到有多种品牌的液晶电视等待测试,其中还包括24和30寸优异液晶显示器。
这块8600GTS正在进行HDMI接口测试,可以看到音频输出测试也并没有被忽视,工作人员专门从主板引出了一条音频线接入显卡的SPDIF接口,从而检验HDMI的音频输出是否正常。
前面的完整性和功能测试属于生产线的重要环节,基本上每块显卡都需要进行这样的流程才能通过。而接下来有更严酷的测试等着这些显卡,但由于测试需要耗费大量的人力、物力和时间,而且显卡可能会在严酷的测试中损坏、老化,因此只能是抽样检测,无法做到100%全检。
● 第九步:最后抽样检测,全方位测试
抽样检测是按照一定的原则进行,比如从一批500块显卡中随机挑选32片进行测试,如果其中有一块没有经过这些极限测试的考验,那么整批500块都会被当作不合格产品处理,进行更深层次的测试并且分析出现问题的原因。
最后的测试项目主要包括以下内容:
- 硬件兼容性测试:和市面上主流芯片组主板的兼容性
- 软件兼容性测试:模拟普通2D使用、3DMark系列、热门游戏、HDTV等
- 四脚测试:高低温、高低压反复冲击
- 模拟老化测试:5年寿命加速实验
- 连续开关机测试:频繁的瞬时电流冲击
- 疲劳测试:长期高温环境下的稳定性
- 超频测试
- 电磁干扰测试
这部分抽样检测设计的内容也是非常多,其中很多测试项目都是柏能独创的、被很多国际大厂所承认的测试标准,只有经过层层严酷测试,才能数十年如一日的为用户奉献高品质的显卡。因此在我们另外一篇文章中将会对这些测试项目进行详细介绍——“想要出厂这么难?一流显卡质检大揭秘”。
● 第十步:封包、装箱、出厂
最后一步就没有必要多做介绍了,栢能工厂的OEM订单是源源不断,这些为别家代工的显卡只需要简单的工业包装即可出厂,而对于自家的索泰显卡来说,进入零售市场之前就需要好好包装一番了。
索泰显卡的包装设计风格如何暂且不谈,其包装上清楚地印有显卡的所有规格,这一点给用户选择时提供了很大的便利,另外索泰附送的显卡配件非常丰富,DVI转接头、HDMI转接头、SPDIF线、分量、电源等等一应俱全,各类用户都在无后顾之忧。
● 总结——高品质显卡是这样炼成的
之前备受好评的ATI原厂卡和蓝宝石显卡就是出自柏能之手,其实通过前文的图片我们可以发现,柏能拥有非常丰富的产品线,ATI“原厂”的HD2900XT、HD2600XT和蓝宝石的X1950PRO、HD2600PRO都在大量生产,柏能为了确保A卡产量不受影响,为索泰显卡新开了数条流水线,产能非常充足。
通过仔细了解柏能工厂生产显卡的全部过程可以发现,显卡制造的复杂程度其实并不高,也很容易理解。但最难能可贵的的就是厂家在保证显卡品质上所花费的硬功夫:严格的流程管理、制程控制、实时监控和检验测试,每个生产过程都会搭配相应的质量检测,最后还会进行更加严酷的品质测试。
这些对客户、对消费者负责任的态度正是柏能科技获得国际大厂一致好评的秘诀,如今柏能面向零售市场推出自有品牌的索泰显卡,相信柏能强大的设计研发实力以及品控能力,对于打造高品质的索泰品牌大有裨益,也有助于用户接受全新的索泰显卡!<
关注我们
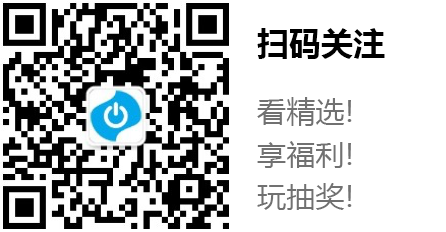